What Is the Economic Order Quantity? EOQ Formula, Calculator, Example
Businesses can use the EOQ to figure out the ideal number of units they should order in order to keep costs low.
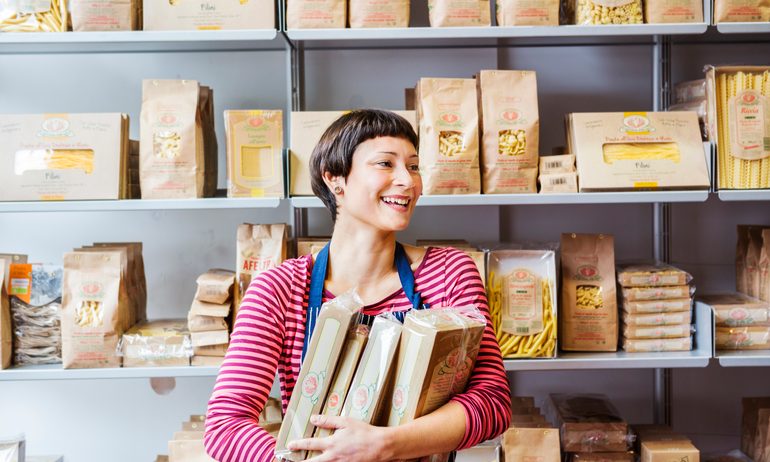
Many, or all, of the products featured on this page are from our advertising partners who compensate us when you take certain actions on our website or click to take an action on their website. However, this does not influence our evaluations. Our opinions are our own. Here is a list of our partners and here's how we make money.
The economic order quantity, or EOQ, is the optimal number of units a business should purchase when replenishing inventory while minimizing inventory costs that could eat into profit margins.
In many cases, you can incorporate the EOQ of a product into a point-of-sale system. The EOQ formula is one of several inventory calculations that small businesses can use to make their inventory management workflows more efficient.
What is the EOQ formula?
To calculate the economic order quantity, you can use the following formula:
![EOQ = √ [ (2 x D x S) / H ]](https://www.nerdwallet.com/assets/blog/wp-content/uploads/2022/03/eoq-formula-320x92.png)
Here’s what those variables mean:
D refers to the annual demand for your product, or how many units you sell per year.
S refers to the setup cost per order, or how much it costs to place each order.
H refers to the holding cost per unit on an annual basis.
When you put that all together, the EOQ is the square root of [(2 x Demand x Setup cost) / Holding cost].
Why do businesses use the EOQ?
The EOQ tells a business the number of items it should order, and it is designed to balance the two inventory costs that businesses incur: setup costs and holding costs.
The setup cost, or ordering cost, is the amount of money a business spends to create and process each purchase order, but it does not include the cost to purchase the goods themselves. Some examples of setup costs include shipping and handling fees, as well as the salaries paid to employees who stock the items upon arrival.
The holding cost, or carrying cost, refers to how much a business pays to store its unsold inventory. These costs can include depreciation, rent for warehouse storage space and the cost of insurance and security.
These two types of expenses are competing costs. By placing a large batch order at once, you would be able to save on your setup cost. But if you order more than you can sell, you will start to rack up holding costs. Businesses use the EOQ formula to help them reduce their overall inventory costs.
» MORE: Best small-business apps
Example of EOQ formula calculation
For example, let’s say you own a successful business that sells duffel bags. Based on your historical data, you know the following information:
Units sold per month: 250.
Setup cost per order: $45.
Annual holding cost per unit: $3.
Here’s how you would take that information to calculate your EOQ for duffel bags:
Find your annual demand: 250 duffel bags x 12 months = 3,000 duffel bags.
Plug your numbers into the formula: EOQ = √ [ (2 x 3,000 x 45) / 3 ] = √ [90,000] = 300 units.
Round up to the nearest whole number. Because the EOQ formula deals with square roots and division, it’s likely your result will include decimals or fractions.
Drawback of the EOQ formula: The annual timeline
You probably noticed that some of the variables require information on an annual timeline. That’s because the EOQ formula makes certain assumptions that demand, setup costs, holding costs and goods prices are always constant.
The formula does not account for things like seasonality trends, bulk order discounts or the supply chain disruptions that we are facing during the pandemic. But you can always make tweaks to the inputs based on your own situation.
How do you use the EOQ formula in your business?
Pair it with another inventory formula. The EOQ formula can be paired with the reorder point formula, which helps a business identify when it should order more inventory. Using these calculations together can help a business avoid running out of stock for its products without carrying more inventory than it needs to.
Use the results to make purchase orders. The EOQ tells you how much of a product you should order, so you can easily use that number when manually creating purchase orders in your POS system, if it has that functionality. But there are also ways to use the EOQ with reorder points to streamline your inventory management workflow.
Set reorder points with your POS system. Many POS systems allow you to set reorder points, or inventory thresholds that indicate when to order more stock. When your product inventory levels reach their reorder points, you’ll be prompted to place another order.
POS systems, such as QuickBooks Desktop Point of Sale, can use reorder points to automate purchase order forms for you, which makes it simple for you to use the EOQ. Some systems, such as Lightspeed Retail’s POS system, will even let you set your desired inventory levels ahead of time.
Product | Starting at | Promotion | Learn more |
---|---|---|---|
![]() QuickBooks Online NerdWallet Rating Learn more on QuickBooks' website | $35/month Additional pricing tiers (per month): $65, $99, $235. | 50% off for first three months or free 30-day trial. | Learn more on QuickBooks' website |
![]() FreshBooks NerdWallet Rating Learn more on FreshBooks' website | $21/month Additional pricing tiers (per month): $38, $65, custom. | 70% off for 4 months. 30-Day Money Back Guarantee. | Learn more on FreshBooks' website |
![]() Xero NerdWallet Rating Learn more on Xero's website | $20/month Additional pricing tiers (per month): $47, $80. | 90% off for 6 months. | Learn more on Xero's website |
![]() Zoho Books NerdWallet Rating Learn more on Zoho Books' website | $0 Additional pricing tiers (per month): $20, $50, $70, $150, $275. | 14-day free trial of the Premium plan. | Learn more on Zoho Books' website |